DHApps
Customer location: Brazil, South Africa, Egypt, Serbia, Poland, Czech Republic, Netherlands, Russia, Myanmar, Vietnam, India, Spain, Portugal
Application type: Mobile, web and desktop
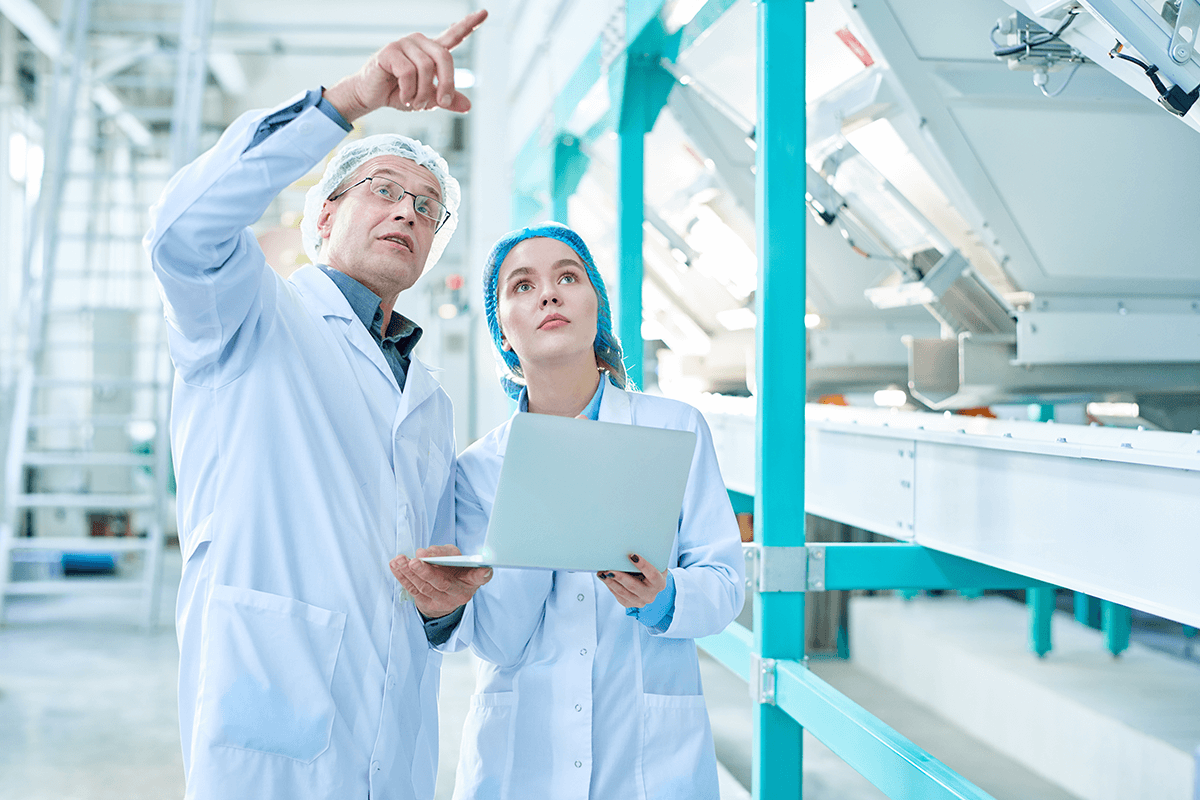
A comprehensive solution for an international manufacturing company
For an international client, we created a comprehensive solution for managing a manufacturing company. The implemented ERP system and dedicated applications unified the operation of the entire company, enabling, among other things, rapid data exchange between branches and headquarters. They also improved the efficiency of factories, supporting their work in real-time and giving full control over production processes.
Challenge:
- The factories within the group used different IT systems or no IT systems at all.
- In some factories, ERP systems were used only for tasks performed by selected departments, not the entire factory, so most work had to be done manually or with spreadsheets.
- It was becoming increasingly difficult to manage the flow of information in the growing group, and sending large amounts of data and reports via email would be time-consuming and inefficient.
- The new system had to adapt to the group’s new organizational structure.
- The system also needed to be adapted to local legal requirements (e.g., the Accounting Law) and guarantee to keep up with their changes in the future.
- It was necessary to adapt the appearance of the printouts and the interface of the implemented software to the conditions of each region where the company’s branch was located.
Goals to be achieved:
- To standardize the IT system across the group.
- Tailoring the system to the characteristic processes of the feed industry.
- Improvement of factory efficiency, maximum automation and integration of processes.
- Availability of advanced but easy-to-use reporting and analytical tools to support decision-making processes, with the aim of controlling production profitability, costs and cash flow.
- Support for real-time work in the areas of the warehouse, sales, production, logistics, HR and payroll, accounting and customer relationship management.
- Easier planning and full control of the production process.
Solution: in those factories that did not have an IT system at all, ERP software was implemented. In addition, dedicated IT solutions were created for the entire group.
Bespoke IT solutions – DH Apps suite:
DH Holding – desktop software for the company’s headquarters, the highest level of the DH Apps suite. Collects information coming from the entire company. It enables centralized management of the company’s strategic data (MDM – Master Data Management) and maintains specified standards throughout the corporation.
The data is properly validated, filtered and distributed to the company’s branches in 13 countries on 4 continents. The collected information is displayed in the form of extensive reports for quick analysis.
The advantage of the application is easy integrability with other systems
DH Country – the second floor in the DH Apps architecture. The main purpose of the application is to manage the company’s strategic data within each country, ensuring consistency across multiple factories.
It is a dedicated desktop system that allows two-way communication: with systems at factories and the headquarters system. DH Country offers a range of reports from data collected at the country level. The system was designed and built to easily integrate with the ERP systems of various suppliers at the level of files, orders and logistics documents. This requirement was crucial and was driven by the need to provide dedicated industry solutions, which are often missing from off-the-shelf ERP systems on the market.
DH Plant, DH Holding, ERP systems from different manufacturers
DH Plant – a dedicated web and mobile application, operating on a single factory level. The system supports the complex management of a factory producing feed or other finished products according to recipes.
The system includes the following independent modules:
Storage module including compartmentalization and storage areas.
Production module within the received recipe and comprehensive management of the packaging process, product batch and delivery settlement.
The quality control module inspects according to the provided quality standards of raw materials and finished products.
The module handling the entry and exit of the car (or other means of transport).
Integration module with external systems (DHC master system, PCS, LIMS).
Do you need a system to manage an international company?
Get a free consultation with our specialist
Write usAmong other things, the system allows users to:
- recording purchases/acceptances and releases/sales, thanks to integration with weighbridges, it is possible to automatically record the weight when a production plan is adopted,
- recording production,
- recording of samples taken and laboratory results, management of test results (acceptance, rejection of results) and transfer to other factories for testing at other locations
- grouping, combining samples (multiple silos on a car, multiple production batches),
- recording data from an external production system (PCS),
- warehouse management software – a map of the warehouse with detailed information on the location of goods,
- control of batch paths of goods from purchase, through storage and production, ending with sales,
- identification of goods based on unique bar codes,
- mobile work used in production, sales, and inventory.
- DH Country, PCS production management system, laboratory system, weighing scales
- mobile devices
Success:
- increase in productivity
- reduction of production cycle time
- reduction of unplanned and planned downtime
- reduction of production costs
- increased utilization of production capacity
- optimization of the use of production resources, thanks to their precise balancing by the system, taking into account the production recipes received from the headquarters
- control over the processes in all factories
- easy and quick identification of each commodity
- transparent results of quality tests allowing quick appreciation of assessments
- centralization of data
- facilitated and unified reporting to headquarters, as well as subsequent aggregation of information flowing from factories
- filtering of data by individual factories
- support of the decision-making process through access to advanced analyses and reports created ad hoc, without the help of the IT department
- automation of business processes
- forecasting of economic indicators and control of realization of the company’s strategy
- ongoing control of revenues and costs by individual branches and other cost centres
- unification of business processes
- access to up-to-date counterparty data, including in particular billing, credit limit and transaction history
- quick flow of information and central control over processes taking place in branches and factories
- increased level of customer service, thanks to full and widely available information on customer preferences, orders and contact history
- integration with external ERP systems
- easy administration of the system from the head office level
Customer Opinion
Management of De Heus Nutrifarms
Kotrak’s extensive experience in the agri-food industry allowed for the comprehensive and professional computerization of our company to the expected extent.
The expertise and technical knowledge of Kotrak’s implementation team allowed the introduction of properly tailored IT solutions, which is something that deserves full recognition.
Reynauld van Rooyen
IT Manager, De Heus Feed Ltd.
The system has been tailored to our needs and supports management in production and logistics processes, sales and warehouse management. The implementation has also increased the efficiency of the accounting department.
Thanks to user-friendly and advanced Business Intelligence tools, multidimensional reports and analysis are at everyone’s fingertips. As a result, decision-makers spend less time searching for information and can focus on strategic decisions.
Piotr Łuczak
Deputy CEO of De Heus Ltd.
Thanks to insightful pre-implementation analysis and the experience of Kotrak consultants with knowledge of industry processes, we were able to achieve our goals.
The implemented system provides us with data integrity, process automation and support in decision-making based on operational (sales, purchasing, warehouse, production) and financial analyses.
Discover our range of dedicated applications
Chemical Manufacturing Software
Run your laboratory, production and warehouse with flexible software created especially for chemical industry!
Check it outFood Manufacturing Software
Take control of your entire food production process, from the moment materials enter your facility through to final product delivery!
Check it outKotrak Warehouse Management Software
Keep track of all your products in real time and strengthen your workflow processes!
Check it outLooking for a dedicated solution for your business?
Contact us