Digital twin in logistics and warehousing
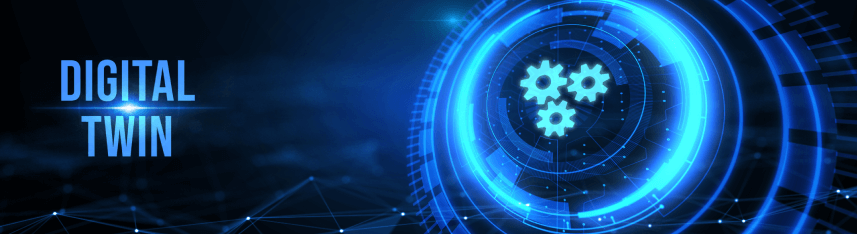
Digital twin is one of the tools that really improves operations in many industries. It is no different in logistics, where the use of digital twins is becoming increasingly popular. Digital copies of real objects (buildings, machines, vehicles, etc.) or processes can introduce many optimizations to real life. In our entry, we will look at how digital twins support the optimization of logistics processes.
Our article will introduce you to the following topics:
A digital twin is a virtual replica of real objects. It is created to perform digital simulations that can be performed any number of times, which reduces the need for physical prototyping. Digital twins are created based on:
In the logistics industry, digital twins are used in a variety of ways. One example of the use of digital twins is supply chain management, e.g. in the pharmaceutical or food industry. Digitalization of the supply chain can cover every element, from production, through customer demand, to inventory. A supply chain twin makes it easier to predict demand growth and plan in such a way as to best respond to recipients’ interest. Additionally, digital twins in transport enable full tracking of loads, i.e. their location, status or storage conditions, which is particularly important for logistics companies transporting food or medicines. Digital twins in inventory management are useful for monitoring the condition of stored products, because they can detect spoiled goods early enough.
Conclusions drawn from data analysis allow for optimizing the logistics process and increasing work efficiency. Digital twins of logistics also provide the possibility of more efficient management of the transport fleet. In addition to the fact that they can monitor real-time data on fuel consumption and components (digital twins in predicting failures and maintaining traffic), they can also optimize the route of the journey. The complexity of the possibilities of using a digital twin in logistics means that the option of creating completely autonomous logistics systems is increasingly being discussed.
Another place where digital twins will be used is maritime transport. Ships that have to sail on long and often dangerous routes will particularly benefit from the use of this modern digital technology. The use of a digital model, as well as subsequent monitoring and maintenance of traffic, help to significantly increase operational efficiency. A specific unit is returned 1:1 in a virtual replica, also taking into account the volume of containers or cargo. Then, data related to the maintenance and voyage of the vessel is analyzed, such as:
Ports also use the digital twin in logistics, including those in Rotterdam and Livorno. The twin can represent the quay or cranes, but also port operations (a twin of the logistics process), for example by simulating the necessary cargo handling and planning warehouse processes. Simulation of logistics processes allows for the identification of potential problems and optimization of workflow before they are implemented.
Digital twins are also revolutionizing other areas of work in the port – so-called “digital dolphins” have been created. They were created by placing.
Digital twins in warehouses are of course another way to use this useful technology. As in other cases, digital twins can support various areas, both in terms of real objects and entire warehouse processes. Importantly, a digital twin can also be used where the real object does not yet exist. For example, if a new warehouse is planned, the digital twin can help verify every aspect of its operation, long before construction begins.
Using a digital warehouse model makes it easier, for example, to assess the construction of racks and the level of safety for warehouse employees, e.g. during earthquakes, but also in everyday work, when stability and compliance with applicable regulations or ISO standards are of great importance. Digital twins in warehouse design can also support the optimal use of space so that as much goods as possible fit into the hall. Another option is to optimize warehouse processes so that the path to the picked product is as short as possible, which shortens the picking time.
Digital twins in the simulation of warehouse processes can find bottlenecks and enable the optimization of logistics processes, for example by suggesting changes in stocking in real time in relation to increases in demand. The advantage of digital twins is that the warehouse manager can test the digital model and run simulations as many times as he wants and in any way he wants, without interfering with the real, ongoing activities. This improves both individual warehouse processes (such as generating picking lists or picking goods), as well as the connections between them. Digital twins are also extremely useful in efficiency analysis and monitoring KPIs.
Digital twins can additionally automate work in the warehouse and learn on an ongoing basis to operate even better based on data and simulations. With the help of artificial intelligence, tasks for autonomous vehicles can be effectively planned and specific, repeatable activities can be indicated for them to perform, and then they can be planned in such a way that they do not conflict with the work of people on the floor. Warehouse process planning can also include automatic collection of data on the location of specific goods and forklifts, and then sharing detailed information with warehouse or transshipment terminal employees.
A digital twin also allows for more effective implementation of a WMS system by simulating possible solutions in digital reality, before the software is actually implemented. Digital simulation helps avoid potential errors and shortens the configuration time, and can also be a backup copy of the real system. Another advantage is the ability to conduct training for new employees in a virtual warehouse replica before they start performing their tasks on the floor. This reduces the risk of making a mistake during real picking.
Choose your IT system through consultation with our specialist
Write to us!There are many advantages of digital twins in logistics. Below we will list the most important ones:
Digital twins in warehouses and logistics mean a lot of benefits, but there are also a few elements worth paying attention to. The first is the issue of knowledge resources – the market does not yet have easy access to many specialists who have experience in creating a digital twin in logistics. It is therefore worth finding out exactly what skills your IT partner has.
Another issue is the skillful integration of the digital twin concept into the overall company strategy, and later – the involvement of employees in the process of implementing this digital solution. At first, it may seem unprofitable or difficult to use, but in the long run it brings significant savings and is a source of invaluable help. The change in the approach to work must cover both ordinary employees, who must understand the meaning of collecting data, and the company’s management, who must learn to make decisions based on a completely different way of doing business.
It must be admitted, however, that there are so many advantages to implementing a digital twin that it is worth preparing really well for its implementation in order to gain the full benefits.
Write to us!
A digital twin is a concept that allows companies in many industries to make valuable improvements, as well as save money. In our post, we outline specific applications of digital models and the benefits of introducing digital twins in various areas of business conducted.
Read moreWhen preparing to implement an IT system for a company, special attention should be paid to the pre-implementation analysis. This is an important stage of the project, which is not only responsible for the correct configuration of the programme, but also allows you to optimise the operation of the entire enterprise, and this in several ways. In today's article, we take a closer look at the benefits of performing an analysis and show how wide-ranging its impact is on the smooth progress of the implementation.
Read moreDo you want to streamline processes in your company and are looking for a personalised solution? Dedicated software allows you to automate many tasks, optimise the work of your team or create modules that streamline your work making it more efficient.
Read more